再见!高价SiC—迪思科开发出产量增至1.5倍的晶圆加工技术
摘要: 迪思科(DISCO)开发出了利用激光从SiC铸锭上切割SiC晶圆的新工艺“KABRA”。与使用线锯的传统方法相比,生产SiC晶圆的加工时间大约可以缩短到1/4,产量大约可以增加到1.5倍。
迪思科(DISCO)开发出了利用激光从SiC铸锭上切割SiC晶圆的新工艺“KABRA”。与使用线锯的传统方法相比,生产SiC晶圆的加工时间大约可以缩短到1/4,产量大约可以增加到1.5倍。部分客户已经开始试用这次的加工方法。
目前从SiC铸锭上切割SiC晶圆主要使用金刚石线锯。但这种加工方法存在两大课题。1个是SiC非常坚硬,加工时间长。另1个是线锯切割部分的材料损耗大,会减少1只铸锭可以切割出的晶圆数量。这些因素导致了SiC晶圆的生产效率降低,成本居高不下。因而抬高了SiC功率元件的成本。
利用激光设置分离层
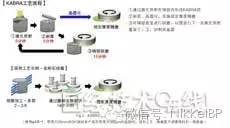
这次的加工方法与传统方法
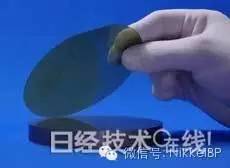
剥离出的口径为4英寸的晶圆
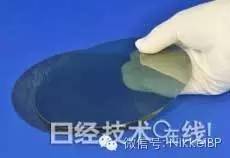
剥离出的口径为6英寸的晶圆
这次的加工方法遵循以下步骤。首先,沿垂直方向,从SiC铸锭的上面连续照射激光。通过这样的方式,设置吸收光的“分离层”。这时可以以任意深度,形成扁平状(激光入射方向与垂直方向)的分离层。接下来以分离层为起点,剥离SiC晶圆的薄层。然后将剥离下来的晶圆研磨成需要的厚度并出货(“规定厚度精磨”)。剥离后的铸锭表面需要另行抛光,以准备下一次的激光照射。通过重复这一连串的操作,利用1只铸锭制作出一片片晶圆。
这种方法与使用线锯的以往方法相比,缩短了加工时间,减少了裁切时的材料损耗。比如说,当使用口径为100mm(4英寸)、厚度为20mm的SiC铸锭,生产厚度为350μm的晶圆时,使用这次的加工方法切割出1片晶圆需要25分钟,加工1只铸锭总耗时约为18个小时。
而使用过去的方法加工1片晶圆大约需要2个小时(1.6~2.4小时),总耗时为2.5~3.5天。使用口径为150mm(6英寸)的SiC铸锭切割晶圆,使用这次的方法大约需要30分钟,而过去的方法需要3个多小时。
材料损耗也较少
不仅缩短了加工时间,而且无需使用线锯加工所需的“磨削”。在线锯加工时,晶圆表面会产生50μm左右的起伏。磨削的作用是去除这些起伏。这次的方法可以抑制起伏,省去了磨削的麻烦。
迪思科表示,使用传统方法时,每加工1片晶圆,线锯切割部分的材料损耗约为200μm。而这次的方法是以分离层为起点剥离晶圆,几乎没有材料损耗。剥离后虽然需要去除分离层,但损耗可以控制在100μm。因此,1只铸锭可以加工出的晶圆数量大约是过去的1.5倍。(记者:根津祯)
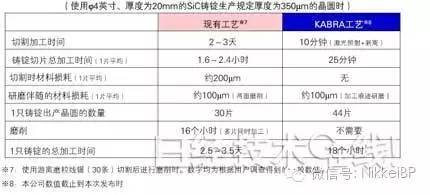
这次的加工方法与传统方法的比较
凡注明为其它来源的信息,均转载自其它媒体,转载目的在于传递更多信息,并不代表本网赞同其观点及对其真实性负责。
用户名: 密码: